丰田生产系统14原则
2020-08-11 14:13作者:admin
丰田生产系统(Toyota Production System,TPS )又名丰田式生产管理(Toyota Management),是日本Toyota汽车副总裁Taiichi Ohno大野耐一所建立现代化生产管理模式,不但结合了丰田集团的Just in Time(简称JIT)即时管理系统与Kanban看板管理两大系统,且加入高度自动化生产与生产制度落实与规划,并已逐渐发展成一套完整包含企业经营理念、生产单位组织、物流及品质管理、成本控制、程式库存管理和生产单位管理的作业体系,能够有效降低企业的生产成本、提高生产效率,且逐步改善产品的生产品质,是目前最受瞩目的企业管理理论之一,也是今天所有管理阶层及管理学院学生都需要深入了解的必修科目。
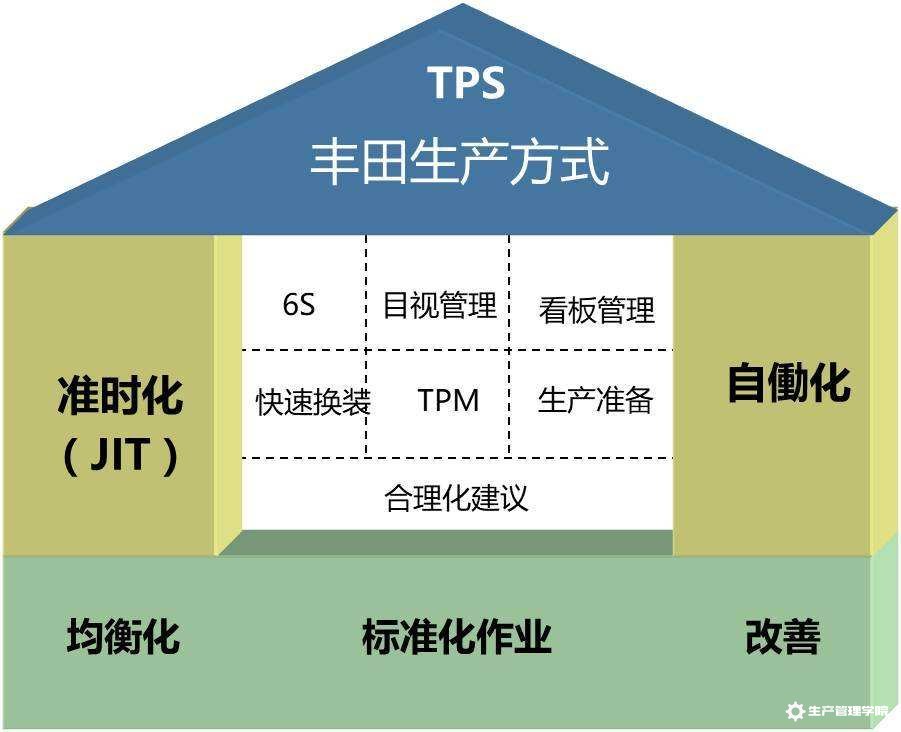
单1目标,2大基础
丰田生产系统是Toyota副总裁Taiichi Ohno大野耐一所建立的生产管理模式,结合了JIT即时管理系统与看板管理,也是让Toyota汽车成为世界第一的重要关键。
丰田生产系统的原理与架构,其实说穿了一点也不复杂,就是透过丰田集团著名的Just in Time(简称JIT)即时管理系统与Kanban看板管理两大系统,并以大量自动化生产模式,降低生产成本、提高效率,并逐步提更产品水准。
如同我们在前一篇文章中所提,Just In Time即时管理系统,是一套以「生产准时」为最高准则,透过「看板」居中协调,并由产品端向原料端提供需求的生产方式,所以能够有效减少生产成本的管理系统,可以永远只保持适当的原料与成品在库,在恰当的时候生产出数量刚刚好之成品,严格控管「浪费」的产生,且比一般传统单一产品大批量的生产方式,更适合市场规模较小或需求多样化的市场。
丰田生产系统除了能够协助管理阶层更轻松地掌握成本,由于生产线上的员工也被赋予了「自主管理」的任务,所以只要发现产品品质或机械与「看板」(图中央上方吊挂的纸张)所记载的内容不同时,都可以立即决定停机、排除故障,以避免生产出瑕疵品、造成成本的浪费。
而且除了能够协助管理阶层更轻松地掌握成本,由于JIT在规划生产线时,生产线上的员工在控制每日产能与需求时,还被赋予了「自主管理」的任务,所以只要一发现产品品质、数量或机械发生异常问题时,任何人当下都可以立即决定停机、察看,主动排除故障,解决问题,以避免生产线上产生多余的浪费,并让工作更有效率。
设立目标,贯彻14原则
也由于Toyota汽车的丰田生产系统不仅成功地让它们有效的减少生产成本,且所生产出来之各式产品,在消费者的评价与客户满意度调查中,也一直拥有不错的回应,甚至让原本仅是「日本第一」的Toyota,逐步成长成今天的「世界第一」,并吸引国内外各大管理学院纷纷开课研究箇中奥秘,美国知名工业工程管理学教授Jeffrey Liker还将其生产线的管理理念,重点式的归纳成14项原则。
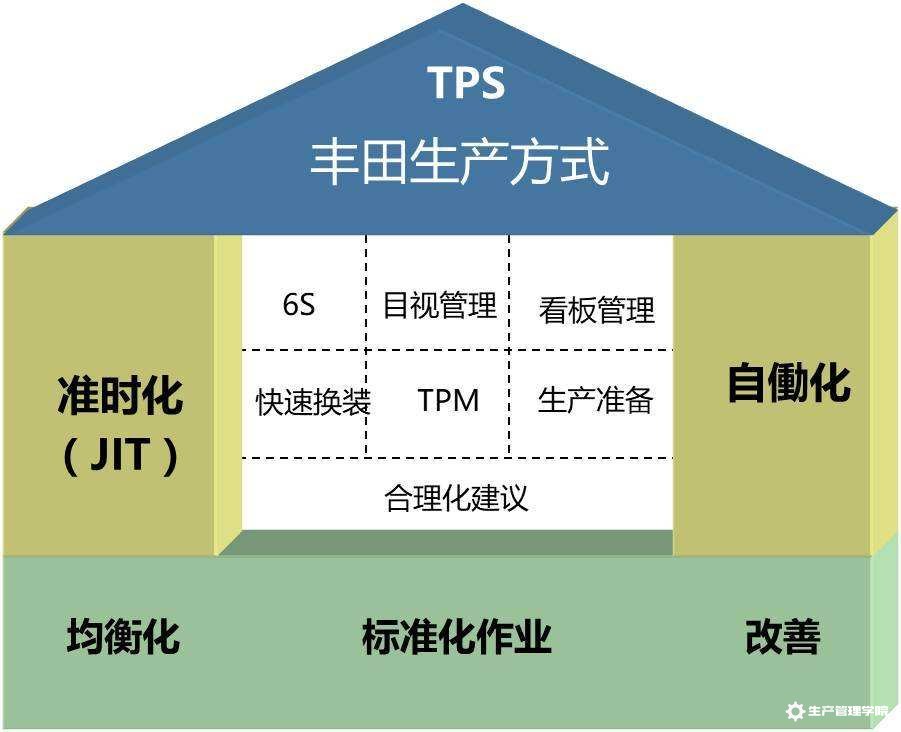
单1目标,2大基础
丰田生产系统是Toyota副总裁Taiichi Ohno大野耐一所建立的生产管理模式,结合了JIT即时管理系统与看板管理,也是让Toyota汽车成为世界第一的重要关键。
丰田生产系统的原理与架构,其实说穿了一点也不复杂,就是透过丰田集团著名的Just in Time(简称JIT)即时管理系统与Kanban看板管理两大系统,并以大量自动化生产模式,降低生产成本、提高效率,并逐步提更产品水准。
如同我们在前一篇文章中所提,Just In Time即时管理系统,是一套以「生产准时」为最高准则,透过「看板」居中协调,并由产品端向原料端提供需求的生产方式,所以能够有效减少生产成本的管理系统,可以永远只保持适当的原料与成品在库,在恰当的时候生产出数量刚刚好之成品,严格控管「浪费」的产生,且比一般传统单一产品大批量的生产方式,更适合市场规模较小或需求多样化的市场。
丰田生产系统除了能够协助管理阶层更轻松地掌握成本,由于生产线上的员工也被赋予了「自主管理」的任务,所以只要发现产品品质或机械与「看板」(图中央上方吊挂的纸张)所记载的内容不同时,都可以立即决定停机、排除故障,以避免生产出瑕疵品、造成成本的浪费。
而且除了能够协助管理阶层更轻松地掌握成本,由于JIT在规划生产线时,生产线上的员工在控制每日产能与需求时,还被赋予了「自主管理」的任务,所以只要一发现产品品质、数量或机械发生异常问题时,任何人当下都可以立即决定停机、察看,主动排除故障,解决问题,以避免生产线上产生多余的浪费,并让工作更有效率。
设立目标,贯彻14原则
也由于Toyota汽车的丰田生产系统不仅成功地让它们有效的减少生产成本,且所生产出来之各式产品,在消费者的评价与客户满意度调查中,也一直拥有不错的回应,甚至让原本仅是「日本第一」的Toyota,逐步成长成今天的「世界第一」,并吸引国内外各大管理学院纷纷开课研究箇中奥秘,美国知名工业工程管理学教授Jeffrey Liker还将其生产线的管理理念,重点式的归纳成14项原则。
丰田生产系统14原则
原则1:企业经营与生产线需设立长远目标
尽管大野耐一所提出之丰田生产系统的终极目标是降低生产成本,但他也认为,企业虽然要尽力降低生产成本,但降低成本绝非短期目标,而是应该将它视为公司长远的政策,所以就算短期目标可能会产生一些浪费,但若是能够促进公司的永续成长,部分成本的发生是可以被允许的。
原则2:采用「向前的生产流程」
与一般生产流程不同,丰田生产系统改变了传统生产过程从原料开始的工序,改以根据当天预期所需完成的产品产量而向前规划工序,不但能够减少原料库存,更重要的是,能够让生产单位明确地掌握产量及生产进度。
原则3:建立流畅的作业流程
所谓流畅的作业流程,就是透过良好的安排及规划,把生产线上工作人员及工作站间的闲置或等候时间降至最低,不但能减少人力的浪费,还能提高工作效率。
原则4:工作均衡化
想要创造一个流畅的作业流程,最重要的便是让工作均衡化,因为若工作负荷比重不均,各工作站工作时间便会产生落差,也会使得生产线上发生闲置或中断,自然会出现人力或生产机器的浪费。
原则5:发现问题,即时暂停
让每个生产线上的员工在发现问题时都可以让生产线立刻暂停,其实是丰田集团创办人丰田佐吉观察纺织机运作后所留下来的观念,因为若有一根线断掉而没有员工发现的话,纺出来的布匹其实都是瑕疵品,形同浪费。 所以丰田佐吉才发明了「安灯」(andon)制度,当有员工发现生产线异常时,立刻发出讯号、停机,才能减低不良品出现的机会。
这项发明后来也被导入Toyota汽车,成为丰田生产系统的主要一环,所以生产线上发生问题时,所有员工都有权立即停止生产线,解决问题,以有效减少因瑕疵品所产生的浪费。
原则6:工作标准化
工作标准化虽然会让工作内容有点单调,但相反的,工作内容标准化,却能够让员工持续改善工作的方法,并有效减少错误产生的机会。
原则7:借重「看板」
尽管电脑普及后,「无纸化」作业已成为许多企业内部的目标,但在丰田集团内,他们却坚信员工需以看板上所记载的生产内容为依归,所以在丰田集团的生产线上,到处都有以纸或木板做成的看板在流通,所以一但工作站内的员工发现半完成品与看板上所记载的有所差异,便能够很快地发现其中的错误,并加以除错,降低瑕疵品产生的机会。
原则8:采用最适当的生产技术
与机器相比,人是较容易发生错误的,所以企业应该应该提供员工经过反覆测试、较不容易出错,最适当的生产方式,而不是让员工自己在错误中找出适当的生产方式。 。
原则9:培养真正了解企业文化的员工
丰田生产系统还有一个成功的关键,那就是他们不喜欢从外部挖角,「空降」高阶主管,而是喜欢从企业体内寻找了解公司内部文化的员工,并栽培他们,如此不但能够让员工更有向心力,也能让企业体内的所有员工都能彻底了解丰田生产系统的文化与精随,且在做决策时,能够深刻体会决策是否与公司最高指导原则冲突。
原则10:强调团队合作
由于丰田集团内部的员工都很了解丰田生产系统,且充分相信这套生产模式,所以员工们都相当团结,且愿意执行丰田生产系统。 所以在丰田集团工作的员工,总是都会以身为丰田集团一员为荣,愿意无私的团队合作,以企业成败为己任,也才能有效地强化生产效率、减少问题的发生。
原则11:重视合作伙伴
丰田集团还会把拥有合作关系的企业体视为集团的延伸,并尽可能地在各方面协助它们成长,帮助他们降低成本、提高效率,甚或指导它们采用丰田生产系统,使集团与协力厂商的生产力皆能共同成长,创造双赢的局面。
原则12:亲临现场了解情况
如果你不充分了解实际情况,就无法解决问题与作出改善,这意味你必须追溯源头、亲自观察、深入分析情况,尤其是「现地现物」。 不要只根据别人呈报的资料或电脑萤幕显示的东西作出推论,远距离地解决问题。
在丰田集团,当生产线出现问题时,管理者第一时间通常就是得亲自前往现场,藉由实际观察问题的产生,研究解决之道;而不是只透过生产线员工口述,便轻易提出问题的解决之道,这样才能减少二次问题发生的机会,真正彻底解决问题的发生。
原则13:提出并解决5个W
发生问题后,丰田生产系统内就会先针对问题提出5个W:Why、Who、When、Where与What,再透过集体讨论的方式,在团队内形成共识,再讨论问题可能的解决方法。 这样的解问题方法虽然较花费时间,但却可以从根本中找出问题,并彻底进行解决。
原则14:不断检讨,持续改善
就算生产线运作正常、企业体持续成长,但在丰田集团内这样却是不够的,因为丰田生产系统期望每个员工都能透过不断的学习以持续成长,并时刻反省,甚至在生产过程中找出更适合的作业方法,协助生产线降低生产成本、提高效率,而这也是丰田生产系统的核心价值之一。